 |


<< Назад к списку статей Инновационное развитие производственных предприятий
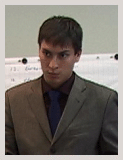 |
 |
Гафитулин Тимур Маратович
НОУ "АТРИЗ"
|
 |
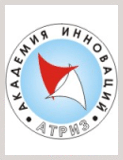 |
 |
Некоммерческое Образовательное Учреждение "АКАДЕМИЯ ИННОВАЦИЙ" (НОУ "АТРИЗ").
Москва, ул. Куусинена, д. 21-Б,
URL: http://atriz.ru/ e-mail: info@atriz.ru
тел. (095) 943-36-66, факс. (095) 754-70-07
Инновации в образовании, семинары практикумы по инноватике, программы подготовки специалистов по инновациям в образовании, менеджменте, промышленности. Консультационные услуги, решение инновационных задач, разработка и реализация инноваций, разработка стратегии опережающего развития.
|
Успешное внедрение ТРИЗ в промышленность сопровождается иногда досадными "проколами", например - в помощи банкротным предприятиям. Но это происходит не по вине АТРИЗ - за все время обучения ТРИЗ в России были охвачены представители сотен промышленных предприятий, но, как это не парадоксально, - среди них не оказалось ни одного из "предприятия - банкрота"!!!
Руководство банкротных предприятий просто не хотело ничего слышать о каких-то консультантах, которые могут поднять завод с колен, не инвестировав в него пару миллионов долларов. И это в то время, когда в ТРИЗ хорошо отработан механизм вывода предприятия из состояния банкротства практически без инвестирования!
За все время внедрения ТРИЗ - всего лишь только четыре предприятия, находящихся на "грани банкротства" (но не "банкроты") - обратились за помощью к ТРИЗ-консультантам - и все четыре вышли из критической ситуации без инвестирования.
Вот простенький пример - для скептиков:
Объединение "Гидростеклоизол" попало в тяжелое экономическое положение:
цены на основное сырье - битум, резко возросли, и выпускать рубероид - основную продукцию - стало экономически невыгодно.
Как быть? Что делать?
Резко повысить цену? - Не будут брать!
- А почему? Ведь охотно покупают подобную финскую продукцию, цена на которую в три раза больше нашей?!
- Да потому, что качество отечественного рубероида - очень низкое: и маленькие отверстия ("микропоры") существуют, и неравнотолщинность слоев битума на подложке есть, и срок службы небольшой, и слипание слоев, и растрескивание от мороза и жары, и много еще других недостатков имеется. И в придачу - высокая себестоимости продукта.
Технология производства рубероида простая: лента из стекловолокна шириной около метра разматывается из рулона, протягивается через высоченную сушильную камеру, затем окунается в ванну с расплавленным битумом, охлаждается специальными охлаждающими роликами, режется на куски и сматывается в рулоны, которые идут на склад.
Предвидя банкротство, специалисты составили бизнес-план, нацеленный на повышение качества продукции и позволяющий удержаться "на плаву".
Резко поднять срок службы рубероида и покончить с растрескиванием можно, если в расплавленный битум добавить и хорошо размешать полиэтилен.
Но расплавленный полиэтилен тяжелее битума, поэтому в существующем на заводе оборудовании (огромный чан с мешалкой в горизонтальной плоскости, наподобие кухонной тестомешалки) он не размешивается, а отстаивается на дне.
Поэтому была предусмотрена покупка специальной финской шнековой мешалки, которая перемешивает массу не только в горизонтальной, но и вертикальной плоскости (стоимостью около 60 тыс.$).
Кроме того, огромная, с трехэтажный дом, сушильная камера, потребляющая более 100кВт электроэнергии на подогрев и вентиляцию воздуха, не обеспечивает надежного удаления влаги из стекловолокна. В результате - дырочки в рубероиде от пара, образовавшегося при вскипании влаги при окунании стекловолокна в расплавленный битум; брак!
Для ликвидации этой неприятности в бизнес-плане было предусмотрено увеличение мощности сушильной камеры до 300кВт, покупка новых вентиляторов и электронагревателей.
Еще больше брака - из-за неравномерного налипания битума на ленту - то много с одной стороны ленты (и мало с другой), то наоборот.
После пропитки в ванне лента с битумом движется горизонтально около 30м., битум стекает вниз, загрязняет ролики. Приходится держать рабочего для ежесекундного контроля за процессом равномерного налипания, управляющего специальными регулирующими роликами.
Поэтому в бизнес-плане предусматривалась покупка дорогой электронной регулирующей аппаратуры для облегчения этой операции.
Когда рулон стекловолокна раскручивается полностью, к нему пришивается нитками начало следующего рулона. На этой операции занят постоянно один работник. Сшивать приходится при движении ленты, а это небезопасно.
Поэтому предусматривалась покупка специального передвижного сварочного устройства.
И множество других бед: слипаются рулоны на складе; мало складское помещение; нет кирпича для стен; и масса других проблем. :Короче говоря, для выхода из "предбанкротной" ситуации предприятию была нужна ссуда в несколько сотен тысяч долларов.
Но только когда все банки и инвестиционные компании отказали предприятию в финансировании этого проекта, руководство обратилось за помощью к ТРИЗ-консультантам.
С помощью ТРИЗ были найдены следующие предельно простые решения, практически не требующие затрат:
- "Наклонить чан для перемешивания битума на 7 град. от вертикальной оси". Для этого под анкерную опору мешалки подложили несколько металлических пластин. Чан наклонился: и полиэтилен начал отлично перемешиваться с битумом! Отпала необходимость в покупке финской мешалки! А это значит - экономия 60тыс.$!
- Огромную сушильную камеру предложили выбросить, вместо нее - поставить небольшое корыто с расплавом дешевой соли. Лента из стекловолокна окунается в расплав, влага мгновенно испаряется - а для поддержания нужной температуры горячего расплава нужно всего около 10 кВт. электроэнергии (вместо 300кВт!). Сушка ленты стала высококачественной, исчез брак "микропоры". Отпала необходимость в покупке ТЭНов и вентиляторов. Освободилась площадь под склад готовой продукции!
- Изменили схему выхода ленты после пропитки ее в чане с расплавленным битумом, с горизонтальной на вертикальную, с центрующими плужками. Битум сам начал равномерно налипать на ленту. Исчез брак по "неравнотолщинности". Рабочий-регулировщик стал не нужен. Отпала необходимость в покупке электронного регулирующего прибора.
- Операцию "сшивания лент нитками" заменили "сшиванием проволочными скобами", наподобие конторского скоросшивателя, только большого размера и большим количеством одновременно загибаемых скоб. Сконструировали и изготовили такой "прибор" прямо на месте, в слесарной мастерской. На "сшивание" двух лент теперь требуется секунды. Отпала необходимость в рабочем - "сшивальщике" и в покупке передвижного сварочного устройства.
- Предложили простые стойки под готовые рулоны рубероида. Рулоны перестали сплющиваться и слипаться; их товарный вид улучшился.
- Для создания временных стен-перегородок в складских помещениях - отказались от покупки кирпича и предложили повесить и скрепить между собой бракованные отсыревшие и
покоробившиеся ленты из стекловолокна, бесполезно лежащего до этого под открытым небом, под дождями и снегом (после чего ленты высохли, распрямились и впоследствии были использованы по прямому назначению);
- Предложили способ для предотвращения "пробок" при подаче расплавленного битума, и т.д. и т.п.
В результате:
- нет брака,
- не нужно переплачивать за электроэнергию,
- снизилась себестоимость продукта,
- качество рубероида резко и многократно повысилось,
- стало не хуже финского,
- теперь можно обоснованно поднять цену.
- Предприятие выбралось из "долговой ямы"- своими силами.
Также в докладе: разбор кейсов ЗАО МПБК "Очаково", Pfaff-Singer, УралТранс.
<< Назад к списку статей << Наверх
|
 |